「品質管理の実践」の範囲の重要語句について,150ページ程度の教科書の内容(第一部:品質管理の実践編)を本記事に圧縮した.学習および復習用としてご活用いただきたい.
勉強法
マークシート方式のため、語句の暗記は必要ない。
それぞれの用語について、概要が思い浮かび、なぜその用語が重要かが分かる状態を目指す。
QC検定2級 他の記事
QC検定2級に関して、他の学習事項についても下記にまとめている。
日本の品質管理の変遷
戦後の日本は品質管理が未成熟で、「安かろう悪かろう」と欧米から酷評された。戦後の品質管理変遷の歴史は出題されることがある。
- 1945年ごろ:統計的品質管理(SQC:Statistical Quality Control)
- 統計的な原理・手法を応用する品質管理の考え方
- 総合的な品質管理(TQC:Total Quality Control)
- 品質管理は企業全体で取り組む必要があるとの考えから生まれた
- 1996年以降:品質管理マネジメント(TQC:Total Quality Management)
品質管理の基礎づくりに貢献した3名(シューハート博士、デミング博士、ジュラン博士)の関連事項は、重要のため整理する。
- デミングサイクル:デミングによる企業内活動の手順
- 調査・サービス:消費者の要求を調査・研究し
- 設計:要求を満足する品質の製品を設計し
- 生産:設計通りの製品を生産し
- 販売:製品を販売する
- シューハートによる管理の定義:ある現象がどう変化するかを予測できる状態のこと
- 工程管理に使用される管理図は「シューハート管理図」とも呼ばれる
- ジュラン:「経営の目的を品質管理だ」とし、生産中心型から市場中心型にするべきと唱えた
- 生産中心型:生産者側の制約を優先する
- 市場中心型:消費者の要求を第一に優先する
品質の概念
品質に関する抑えておきたい語句を列挙する。
- QCD(Quality:品質、Cost:価格、Delivery:納期)
- PSME(Productivity:生産性、Safety:安全性、Morale:モラル、Environment:環境)
- 顧客満足(CS:Costomer Satisfaction):顧客の要望を製品やサービスが満たしていると感じている状態
品質管理に伴うコスト
- 予防コスト(Pコスト:Preventive cost):不具合の予防のためのコスト
- 評価コスト(Aコスト:Appraisal cost):品質維持のための評価のコスト
- 品質管理が不完全であったために被る損失
- 内部失敗コスト(IFコスト:Internal Fault cost):製品出荷前の不良処理のコスト
- 外部失敗コスト(EFコスト:External Fault cost):クレーム・苦情が市場で発生したときの対応コスト
要求品質から品質特性の抽出まで
要求品質から品質特性のブレークダウンの流れ、要求品質→品質要素→品質特性は超頻出。
- 要求品質(Required Quality):市場の品質に関する要求事項
- 顧客の声(VOC:Voice Of Customer)の整理・解析が重要
- 顕在的品質だけでなく、潜在的品質を把握する
- 要求品質展開表:顧客要求から品質要素を整理した表
- 社会的品質:生産者・顧客以外の第三者に産出物が与える迷惑の程度、製造物責任やライフサイクルコスト(LCC)なども含む
- 製造物責任(Product Liability):欠陥製品による損害に対する賠償責任
- LCC(Life Cycle Cost):製品の維持から廃棄までの総コスト
- 顧客の要求品質の1要素となりうる
- 品質要素:要求品質を項目化したもの
- 品質特性:品質要素を客観的に評価できるようにしたもの
- 例:電気製品の安全性の品質要素:絶縁性、漏洩電流、難燃性
- 品質特性展開表:品質要素から重要な品質特性を整理した表
- 代用特性:直接測定が困難な品質要素を、間接的に推定するために評価する品質特性
各フェーズにおける品質
設計品質≒ねらいの品質,できばえの品質≒製造品質は頻出のため,抑える.
- 企画品質:要求品質に対する品質目標、重要度や技術難易度、競合状況を考慮して設定していく品質
- ねらいの品質(設計品質):製造目標として狙った品質
- できばえの品質(製造品質):製造したときの実際の品質、製造品質
製品・サービスの品質充足度と顧客満足の関係
製品・サービスの品質充足度と顧客満足の関係はいくつかに分類できる(狩野モデル:狩野らが『品質』誌に投稿した内容)
- 魅力的品質:充足されれば満足、不十分であっても仕方がない
- 一元的品質要素:充足されれば満足、不十分であれば不満
- 当たり前品質要素:充足されれば当たり前、不十分であれば不満
- 無関心品質要素:充足でも不充足でも、満足も不満も引き起こさない
- 逆品質要素:充足されているのに不満、不充足なのに満足を与える
各品質要素の図示すると次のようになる(理解・イメージのため)
- 横軸:製品やサービスの品質
- 縦軸:顧客満足度
維持と管理
品質の維持・管理に関する語句をまとめる。問題と課題の違いを抑えておけば、語句問題の解の絞り込みに役立つ。
- PDCA(計画:Plan、実施:Do、確認:Check、処置:Act)
- SDCA(標準化:Standardize、実施:Do、確認:Check、処置:Act):維持管理におけるPDCA
- PDCAS(計画:Plan、実施:Do、確認:Check、処置:Act、標準化:Standardize)
- PDCAの後、うまく言っていたときに標準化を行うサイクルのこと
- 問題と課題の違い
- 問題:現状維持のために取り組む必要のある事
- 課題:より良くするために取り組む必要のある事、問題よりもチャレンジングになることが多い
- QCストーリー:品質の問題・課題解決のために行う一連の業務(何度も行うので管理サイクルやPDCAとも言われる)
- 問題解決型QCストーリー:問題(現状維持のため取り組む事項)の原因がある程度分かっている場合のPDCAサイクルを表す
- 課題達成型QCストーリー:課題(より良くするため取り組む事項)達成のために、多くの方策を考え絞り込む必要のある場合のPDCAサイクルを表す
QC的考え方
品質管理において、重要な考え方や概念についてまとめる。
- 品質第一
- 目的志向
- 源流管理:より源流(上流)のプロセスから改善し、効率的に品質保証を管理するしくみ
- 例:設計審査(DR:Design Review)など
- 重点指向:優先順位の高い事項に絞って取り組む
- 三現主義:問題解決の取り組みで、「現場」に行って「現物」を観察して「現実的」に検討すること
- 5ゲン主義:三現主義で問題把握し、「原理」、「原則」に基づいて改善する考え方
- ばらつき管理:ばらつきを抑える基本的手法として管理図がある
- 後工程はお客様:次の工程を含めた後工程全体に喜んでもらう
- プロセス重視:安定した良いプロセスから安定した良い品質が生まれる
- 見える化:対象は問題、プロセス、顧客、知恵、経営など
- マーケット・インとプロダクト・アウト
- マーケット・イン(消費者指向):消費者のニーズ優先
- プロダクト・アウト(生産者指向):生産者の都合優先
- 全部門、全員参加:組織全体が品質管理意識を持つ
- 従業員満足(ES:Employee Satisfaction)
- 人間性尊重:1人1人が創造性を発揮し活躍できる職場づくりや育成を行う
- 自己実現欲求の満足:課題解決に向けて挑戦できる環境、解決されたときの達成感や評価は,従業員満足を高める上で重要
- QCサークル:QCについて自主的に意見交換をし、行動に移していく活動、小集団活動とも呼ばれる
- ハインリッヒの法則(1:29:300の法則)
- 1件の重大な災害・事故に対し、29件の小さな怪我・小事故、300件のヒヤリハットがあったという法則
- 数値(1:29:300)も出題されることがある
ばらつきの要因
ばらつきの要因に関する事項について整理する。
- 偶然原因と異常原因
- 偶然原因:同じ作業をしても発生するばらつき
- 異常原因:標準が守られていない、不備などの要因
- 時系列で分類する要因
- 突然変異
- 散発異常
- 慢性不適合
- ばらつき要因の分類・語句
- 計数的な要因:属性による要因(機械や原料メーカ)
- 計量的な要因:連続値で表せる要因(温度、時間など)
- 4M(材料:Material、機械:Machine、人:Man、加工方法:Method)
- 5M(材料:Material、機械:Machine、人:Man、加工方法:Method、測定:Measurement)
- 4M1E(材料:Material、機械:Machine、人:Man、加工方法:Method、環境:Environment)
品質保証
新製品開発時の品質保証
新製品開発時の品質保証では,企画や設計などの上流工程からの未然防止策(DR, FMEA, FTA)が特に重要である.そのほかの事項もしばしば出題される.
- 品質保証体系図
- 企画・製造から廃棄までで、品質保証活動の全体を示した図
- 縦軸:企画、生産、販売、アフターサービス、廃棄までのステップ
- 横軸:品質保証に関する部門(設計、製造、販売、品質管理)
- 品質機能展開(QFD:Quality Function Deployment):顧客の求める品質を反映させるために、企画設計から生産までの品質保証を行うこと
- 品質展開:要求品質を品質特性に変換
- 技術展開:設計品質を現状の技術・機構で達成できるか検討
- コスト展開:目標コストを要求品質ごとに配分し、コスト問題点を抽出する方法
- 信頼性展開:要求品質から信頼性上の保証項目を明確化する方法
- 業務機能展開:品質を左右する業務の明確化
- デザインレビュー(DR:Design Review):設計段階での品質問題の未然防止・再発防止
- FMEA(Failure Mode and Effects Analysis:故障モード解析):故障の影響、故障の原因・検知方法や対策を事前検討する方法
- FTA(Fault Tree Analysis:故障の木解析):災害やシステム故障から原因を追求していく方法
- 保証の網(QAネットワーク):生産準備段階での品質保証
社会的要求からの品質保証
近年の社会的要求からの品質の要素として,LCA全体でのコストや製造物責任(PL),環境配慮設計(DFE)も求められるようになった.
- ライフサイクルアセスメント(LCA:Life Cycle Assesment):生産から廃棄までの環境負荷を評価するための手法
- 製品安全規制:リスクの高い製品の安全を保障するための技術基準を定め,事故を未然に防ぐための制度
- 製造物責任(PL:Product Liability):製品の欠陥による損害に対する賠償責任
- 製造物責任予防(PLP:Product Liability Provention):PL問題発生の防止、DRや安全性試験がこれに該当する
- 製品安全(PS:Product Safety):PLPの観点からの製品安全対策
- 製造物責任防御(PLD:Product Liability Defence):PL問題が発生しても損失を最小限にする、即応体制や事前準備がこれに該当する
- 環境配慮設計(DFE:Design For Environment)
- 初期流動管理:製品の量産開始後の初期段階における特別な管理体制、通常は最初の2~3ロットのに渡る期間
- 3H(初めて、変化、久しぶり)
プロセス保証と結果の保証
プロセス保証とは「品質は工程で作り込む」という考え方である.
大量生産の時代に沿うように「結果の保証」から「プロセスによる保証」へ変遷している.
- QC工程図(QC工程表、工程管理表):材料の受入から出荷までのすべての工程での品質特性、管理水準・方法を記述
- 工程異常:品質特性が管理水準から外れた状態
- 工程解析:工程における品質特性と要因の解析
- 工程能力:要求品質に対して、ばらつき少なく生産できるかを表す指標(平均値±3σ、6σで表記)
- 作業標準:製造作業の標準
検査(結果による保証)
品質保証では「プロセス保証」に加え,検査による完成製品が品質基準を満たしているかの検査を行う「結果の保証」も重要である.
- 段階による検査の分類
- 受入検査・購入検査
- 工程間検査・中間検査
- 最終検査・出荷検査
- 検査方法による分類
- 全数検査
- 無試験検査:不適合品で次工程に影響がほとんどないときのみ
- 間接検査:受入試験で供給者側の検査成績を書類確認する検査方法
- 抜取検査:全数と無試験の中間、不適合品の混入が許される場合に使用
- 抜取検査の種類
- 計数値抜取検査:サンプルn個抜きとり、そのうち不適合品がc個以内であれば、全数N個(ロット)を合格とする
- 計量値抜取検査:ロットの平均値と標準偏差が基準値以内であれば合格とする(特性値が正規分布に従うときのみ)
- 感性品質:人間の5感(感性)で評価する品質
- 官能検査の種類
- 分析型官能検査:品質特性そのものを5感で測定する検査、人間が測定器の代用のイメージ
- し好型官能検査:人間の感覚状態そのものを測定する検査(例:食品の美味しさ、デザインの美しさなど)
- 計測誤差の解析・評価
- 測定のS/N比
- 測定のS/N比
- 偏り:サンプル平均 – 真の値
- ばらつき:サンプルの不揃い程度(標準偏差)
品質経営
TQM(Total Quality Management)の推進には、方針管理と日常管理の両輪が重要。方針管理は課題解決、日常管理は問題解決(現状維持)のイメージが重要。
方針管理
方針管理は、課題解決を目的とする管理である。
- 方針管理では、重点課題の絞り込みや管理項目が重要
- 方針管理は日常管理よりもチャレンジングで、管理サイクルはPDCAとなることが多い
- 部門横断チーム(CFT:Cross Functional Team)が編成されることもある
- 機能別管理:横ぐし(機能別)の管理 ⇔ 縦ぐし(部門別)の管理
日常管理
通常の業務に対し,標準を順守して現状維持するための管理である。
- 日常管理の管理サイクルは、SDCAとなることが多い
- 管理項目一覧表:各部門での管理項目・管理水準を一覧形式にまとめたもの
- 管理点:結果を確認する項目としての管理項目
- 点検点:要因を確認する項目としての管理項目
- 変更管理:自ら変更した項目の管理(変化点管理との違いに注意)
- 変化点管理:変化の原因が自分以外にある場合の管理
標準化
社内標準、国内標準、国際標準の関連事項についてまとめる。
社内標準化
- 社内標準化の階層構造(下図)
- 製造部門では,作業標準や手順書の他,QC工程図も作成される
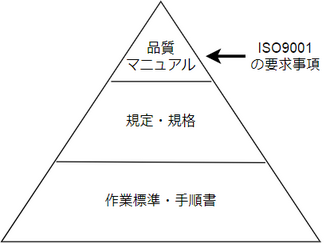
国内規格
JISやその表示制度,認証制度についての内容が出題される.
- 日本産業規格(JIS:Japanese Industrial Standards):製品やサービス、経営管理についての規格
- JISマーク表示制度:製品がJISに適合していることを第三者が証明するための制度
- 継続的に認証維持審査を受ける必要あり
- JISマークの近くに認証機関の名称(略称)の記載必要
- 製品や包装に認証取得事業者の名称(略称)の記載必要
- 3種類のJISマーク

- 試験事業者登録制度(JNLA:Japan National Laboratory Accreditation):産業標準化法に基づき、認証試験を行えるかどうかを第三者が登録する制度
国際標準化
代表的な国際標準化のとしてISOとIECがある.
- ISO(国際標準化機構):電気電子分野以外の広い範囲の国際規格の作成
- IEC(国際電気標準会議):電気電子分野の広い範囲の国際規格の作成
人材育成
OJTやOFF-JT,部門別や職能別の教育方針を抑えておけば十分.
- 職場内教育訓練(OJT:On the Job Training)
- 職場外教育訓練(OFF-JT)
- 職能別教育(横ぐし),部門別教育(縦ぐし)
トップ診断と監査
- トップ診断:経営層が方針管理の一貫として、品質に関する実態を評価する、会議形式や現場調査方式がある
- QC監査:要求品質を満たしているかの検査、取締が目的
品質マネジメントシステム(QMS)
品質マネジメントシステム(QMS:Quality Management System)は,製品の品質を継続的に保つための組織の仕組みである.
次のQMS7つの原則は頻出である.
QMS7つの原則
- 顧客重視:顧客の要求事項を満たす,顧客価値・満足の向上
- リーダーシップ:目的や方針を一致させる
- 人々の積極参加:組織内のすべての階層の力量と権限がある人々の参加が価値創出に不可欠
- プロセスアプローチ:工程やシステムによって品質を作り込む
- 改善:継続的な(品質)改善活動
- 客観的事実に基づく意思決定:データや情報の分析・評価結果に基づく客観的な意思決定
- 関係性管理 :利害関係者(ステークホルダー)との関係のマネジメント
社会的責任
- 企業の社会的責任(CSR:Corporate Social Responsibility)
品質管理周辺の実践活動
マーケティング
- 市場理解の4P(製品:Product、価格:Price、流通:Place、プロモーション:Promotion):
- 顧客から見た4C(顧客課題:Costomer Solution、顧客が支払う費用:Cost、利便性:Convenience、コミュニケーション:Commnication)
商品企画
商品企画については、商品企画の流れと商品企画七つ道具の概要を抑えておけば十分である。
- 商品企画の流れ(市場調査→アイデアだし→アイデア選択→設計)
- 顧客ニーズ調査:確実な調査
- アイデア出し:ユニークな発想が重要
- アイデア選択:最適コンセプトの構築
- 技術・設計への橋渡し
- 商品企画の七つ道具
- インタビュー調査:グループインタビューや評価グリッド法(顧客に比較評価および言語化してもらう)
- アンケート調査
- ポジショニング分析:市場での商品の位置づけを知る
- アイデア発想法:焦点発想法、アナロジー発想法、チェックリスト発想法、シーズ発想法など
- アイデア選択法:アイデアの絞り込み、点数評価表や階層的意思決定法(AHP:Analytic Hierarchy Process)など
- コンジョイント分析:重要要素(価格、色、追加機能など)を抽出し、それらから最適なコンセプトを求める分析手法
- 品質表:コンジョイント分析結果を参考にし顧客の要求品質を分析、設計への落とし込み
- まとめると次の図。商品企画の流れと七つ道具の使いどころが重要。
IEおよびVA/VE
- IE:Industrial Engineering
- 生産技術、生産工学、管理工学、経営工学などの総称
- 現場作業から経営管理までの広い分野で、生産性を向上する手法の総称
- 現場活動のムリ・ムラ・ムダ(3ム)を省く活動
- 価値分析(VA:Value Analysis):組織的な製品の機能分析、最低のコストで必要機能を達成するために行う
- 価値工学(VE:Value Enginnering):VAと同じ
- その他には、設備管理、資材管理、物流・量管理 がある
参考文献
- 教科書(日本規格協会)
- 過去問題集(日本規格協会)
リンク